The Applications of 1.4424 Stainless Steel Bar in High-Strength Equipment Manufacturing
- Share
- publisher
- harris
- Issue Time
- Dec 5,2024
Summary
Discover how 1.4424 stainless steel bars are utilized in high-strength equipment manufacturing. Learn about their properties, applications, and advantages in producing durable, corrosion-resistant equipment.
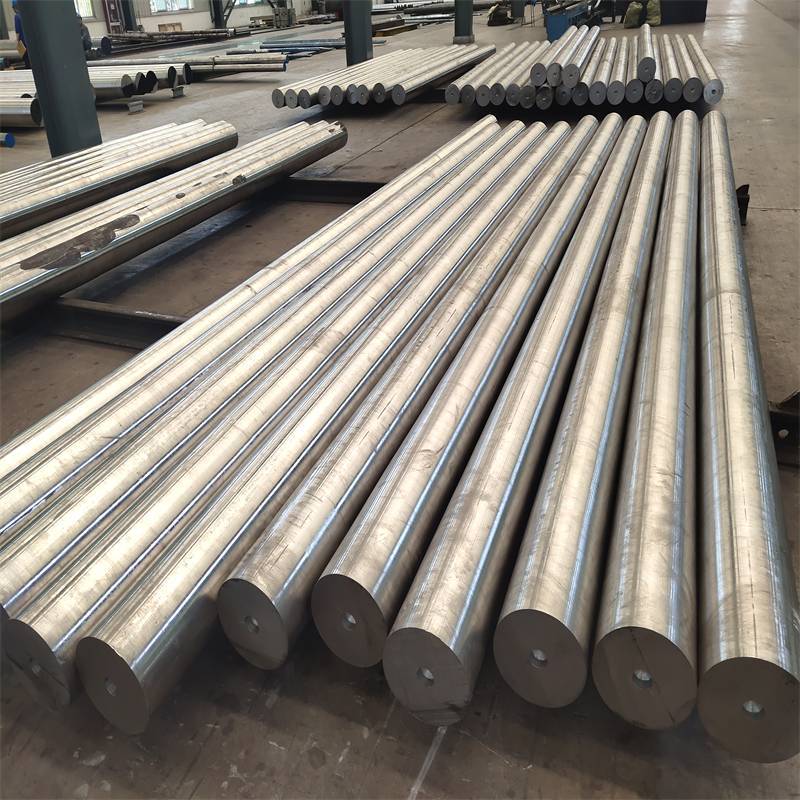
Introduction
In the manufacturing of high-strength equipment, the choice of material plays a pivotal role in determining the durability and reliability of the final product. The 1.4424 stainless steel bar has emerged as a superior material for manufacturers seeking exceptional corrosion resistance and mechanical strength. This stainless steel grade offers unique properties that make it suitable for harsh environments and demanding applications. In this article, we will explore the uses of 1.4424 stainless steel bars in the production of high-strength equipment, highlighting its advantages and the considerations manufacturers should keep in mind.
Understanding 1.4424 Stainless Steel Bar
Composition and Properties of 1.4424
The 1.4424 stainless steel, also known by its designation X2CrNiMo17-12-3, is an austenitic stainless steel grade characterized by low carbon content and the addition of molybdenum. Its typical composition includes:
Chromium (Cr): Approximately 17%
Nickel (Ni): Around 12%
Molybdenum (Mo): About 3%
Carbon (C): Low content, enhancing corrosion resistance
These elements confer several desirable properties:
Excellent Corrosion Resistance: Particularly against pitting and crevice corrosion in chloride environments.
High Mechanical Strength: Suitable for applications requiring robust materials.
Good Formability and Weldability: Facilitates manufacturing processes without compromising structural integrity.
Advantages Over Other Stainless Steels
Compared to other stainless steel bars, 1.4424 offers:
Enhanced Pitting Resistance: The molybdenum content improves resistance in saltwater and chemical environments.
Low Carbon Content: Reduces the risk of carbide precipitation during welding, preserving corrosion resistance.
High Toughness: Maintains strength even at cryogenic temperatures.
Applications in High-Strength Equipment Manufacturing
Oil and Gas Industry Equipment
Downhole Components
In the oil and gas sector, equipment is often exposed to highly corrosive substances and extreme pressures. 1.4424 stainless steel bars are used in:
Drill Collars and Tools: Providing strength and resistance to sour gas environments.
Valve Components: Ensuring reliability in controlling flow under high pressure.
Benefits in the Industry
Extended Equipment Life: Reduces downtime due to corrosion-related failures.
Safety Improvement: Enhances the integrity of critical components.
Chemical Processing Plants
Reaction Vessels and Piping
Chemical plants handle aggressive chemicals that can deteriorate equipment rapidly. 1.4424 stainless steel bars are ideal for:
Reactor Internals: Withstanding corrosive reactions.
Heat Exchanger Tubes: Maintaining performance over time.
Advantages for Manufacturers
Corrosion Resistance: Minimizes contamination and maintains product purity.
Cost Efficiency: Lowers maintenance costs due to longer equipment lifespan.
Marine and Offshore Structures
Shipbuilding Components
Marine environments are notorious for causing metal corrosion. 1.4424 stainless steel bars are utilized in:
Propeller Shafts: Offering durability against seawater corrosion.
Fasteners and Fixtures: Ensuring structural stability.
Offshore Platforms
Structural Supports: Providing necessary strength for heavy loads.
Pipelines: Transporting fluids without the risk of leaks due to corrosion.
Considerations for Manufacturers Using 1.4424
Machining and Fabrication Guidelines
Tool Selection
When working with 1.4424 stainless steel bars:
Use Carbide Tools: For efficient machining and extended tool life.
Optimize Cutting Speeds: To prevent work hardening and ensure smooth finishes.
Welding Practices
Avoid High Heat Input: Preserves corrosion resistance by preventing grain growth.
Use Appropriate Filler Materials: Matching the composition to maintain joint integrity.
Quality Assurance and Standards Compliance
Testing Procedures
Manufacturers should implement rigorous testing:
Non-Destructive Testing (NDT): Such as ultrasonic or radiographic testing to detect internal flaws.
Corrosion Testing: Ensuring material meets the required resistance levels.
Certification and Standards
Adhere to International Standards: Compliance with ASTM, EN, or ISO standards specific to stainless steels.
Material Traceability: Keeping detailed records for quality control and customer assurance.
Conclusion
The 1.4424 stainless steel bar stands out as a material of choice for manufacturers of high-strength equipment due to its exceptional corrosion resistance and mechanical properties. Its applications in industries such as oil and gas, chemical processing, and marine engineering demonstrate its versatility and reliability. By understanding its properties and adhering to best practices in machining and quality assurance, manufacturers can leverage the benefits of 1.4424 stainless steel to produce equipment that meets the highest standards of performance and durability. Embracing this material not only enhances product quality but also contributes to long-term cost savings and customer satisfaction.