What is incoloy 925 alloy? Introduce incoloy 925 alloy application property element
- Share
- Issue Time
- Mar 5,2021
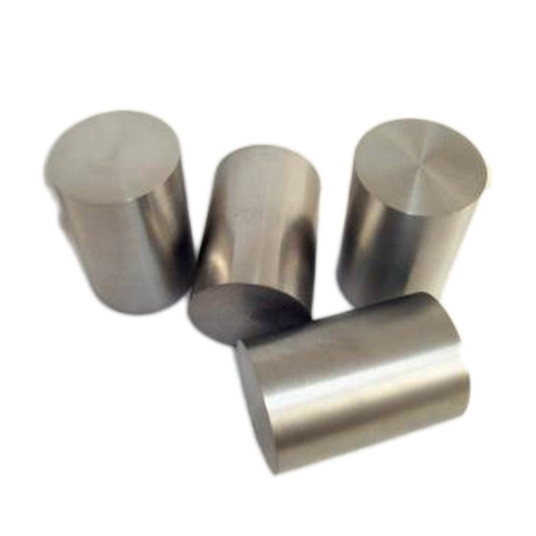
What is incoloy 925 alloy? Introduce incoloy 925 alloy application property element
What is nickel alloy materials?
Nickel alloys are metals made from combining nickel as the primary element with another material. It merges two materials to deliver more desirable features, such as higher strength or corrosion-resistance. Because of its unique properties, it’s used in a variety of equipment spanning multiple industries.
What is incoloy?
Incoloy refers to a range of superalloys produced by the Special Metals Corporation group of companies. They are mostly nickel-based, and designed for excellent corrosion resistance as well as strength at high temperatures; there are specific alloys for resistance to particular chemical attacks
What is the Difference Between Inconel® and Incoloy®?
Although Inconel® and Incoloy® belong to the same family of superalloys, each possesses its own distinct properties, as well as sharing others. Also known as high-performance alloys, the superalloys in general provide high resistance to corrosion and oxidation, as well as mechanical strength at elevated temperatures. The most fundamental of difference between them lies in their composition. Inconel®, predominantly of nickel-chrome, generally contains over 50% nickel, whereas Incoloyl®, a nickel-iron-chromium alloy, has less than 50% nickel content.On a more specific level, the major distinctions between the two are their applications and spheres of suitability.
What is incoloy 925?
INCOLOY alloy 925 is designated as UNS N09925. Designations and specifications for the product include NACE MR-01-75, ASME Boiler and Pressure Vessel Code Case 2218 Section VIII Division 1, and Special Metals Corporation internal specification HA 46. Alloy 925 is available as tube, round bar, flat bar and forging stock.
Where incoloy 925 use to?
INCOLOY alloy 925 is used in various applications requiring a combination of high strength and corrosion resistance. it is used for down-hole and surface gas-well components including tubular products, valves, hangers, landing nipples, tool joints and packers.
Why choose incoloy 925 alloy?
INCOLOY alloy 925 has a high level of corrosion resistance. In both reducing and oxidizing environments, the alloy resists general corrosion, pitting, crevice corrosion, intergranular corrosion and stress-corrosion cracking. Some environments in which INCOLOY alloy 925 is particularly useful are “sour” (H2S containing) crude oil and natural gas, sulfuric acid, phosphoric acid, and seawater.
Incoloy 925 alloy datasheet information
Elements | Content (%) |
Nickel, Ni | 44 |
Iron, Fe | 28 |
Chromium, Cr | 21 |
Molybdenum, Mo | 3 |
Titanium, Ti | 2.1 |
Copper, Cu | 1.8 |
Aluminum, Al | 0.3 |
Carbon, C | 0.01 |
Form/Condition | Tensile Strength | Yield Strength (0.2% Offset) | Elongation | Hardness* | ||
ksi | M P a | ksi | M P a | % | Rockwell | |
Round/Solution-Annealed | 99.3 | 685 | 39.3 | 271 | 56 | 76 B |
Round/Solution-Annealed and Aged | 167.3 | 1154 | 120.6 | 832 | 27 | 32 C |
Cold Drawn Tubing/Solution- Annealed and Aged | 172.5 | 1189 | 120.4 | 830 | 27 | 35 C |
Incoloy 925 alloy heat treatment
Solution annealing in preparation for age hardening should be done at 1800-1900°F (980-1040°C) for a minimum of 30 min and a maximum of 4 h. Cool at a rate equivalent to air cooling, or faster, for sizes of 1 in (25 mm) or under. Water quench all sizes over 1 in (25 mm).
The following age hardening treatment is normally used: 1350-1380°F (732-749°C)/6-9 h, FC to 1150°F (621°C), hold at 1150°F (621°C) ± 15°F (8°C) for a total aging time of 18 h. Cool at a rate equivalent to air cooling, or faster.
Incoloy 925 alloy conclusion
The Incoloy 925 nickel content is sufficient for protection against chloride-ion stress- corrosion cracking. The nickel, in conjunction with the molybdenum and copper, also gives outstanding resistance to reducing chemicals. The molybdenum aids resistance to pitting and crevice corrosion. The alloy’s chromium content provides resistance to oxidizing environments. The titanium and aluminum additions cause a strengthening reaction during heat treatment.