CLASSES OF STAINLESS STEEL
- Share
- Issue Time
- Sep 13,2022
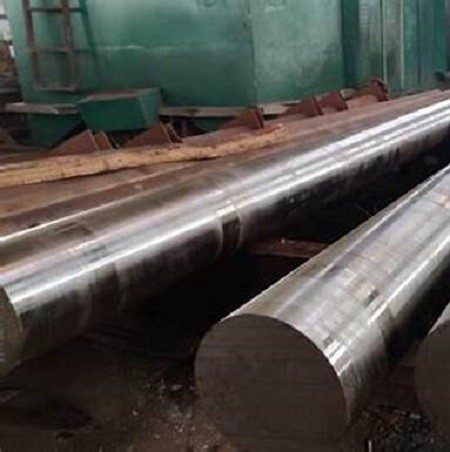
CLASSES OF STAINLESS STEEL
What is Stainless Steel?
Stainless steel is a low carbon steel which contains chromium; it is this addition of chromium that gives plain steel its unique stain and corrosion resisting properties. The chromium in the steel allows the formation of a rough, invisible, corrosion resisting chromium oxide film on the steel surface. If the material is damaged either mechanically or chemically, the film heals itself (providing that oxygen is present). With the addition of chromium and other elements such as molybdenum, nickel and nitrogen, the steel takes on increased corrosion resistance and other properties.
The Classes of Stainless Steel
Stainless steels are generally grouped into 5 different classes. Each is identified by the alloying elements which affect their microstructure and for which each is named.
Martensitic stainless steels
Ferritic stainless steels
Austenitic stainless steels
Duplex (ferritic-austenitic) stainless steels
Precipitation-Hardening (PH) stainless steels
Martensitic Stainless Steel
Martensitic Stainless grades are a group of stainless alloys made to be be corrosion resistant and harden-able (using heat treating). All martensitic grades are straightforward chromium steels without nickel. All of these grades are magnetic. Martensitic grades are mainly used where hardness, strength, and wear resistance are required.
Grade Types
Type 410: A basic martensitic grade that contains lower alloy content. It has a relatively low cost, and it is a general purpose, heat treatable stainless steel. Typically used where corrosion is not too severe (such as air, water, some chemicals, and food acids.). Applications for this product can include parts needing a combination of strength and corrosion resistance, such as fasteners.
Type 410S: Holds a lower carbon content than Type 410, but provides improved weldability with lower hardenability. This is a general purpose corrosion and heat resisting chromium steel.
Type 414: This type has increased Nickel content (2%) for improved corrosion resistance. Typical applications include springs and cutlery.
Type 416: The added Phosphorus and Sulphur in this type allow for improved machinability. Typical applications include screw machine parts.
Type 420: Increased carbon in this type helps improve the mechanical properties. Typical applications include surgical instruments.
Type 431: Has increased chromium content for greater corrosion resistance and good mechanical properties. Typical applications include high strength parts such as valves and pumps.
Type 440: Further increases to the Chromium and Carbon content help improve toughness and corrosion resistance of this type. Typical applications include surgical instruments.
Ferritic Stainless Steel
Ferritic Stainless grades resist corrosion and oxidation, whilst remaining resistant to stress and cracking. Although these steels are magnetic, they cannot be hardened using heat treatment. Once annealed these grades can be cold worked. They have a higher corrosion resistance than martensitic grades, but are mostly inferior to the austenitic grades. These grades are straight Chromium steels with no Nickel, and are often used for decorative trim, sinks, and certain automotive applications such as exhaust systems.
Type 430: A basic grade that has less corrosion resistance than Type 304. This type has a resistance to corrosives like nitric acid, sulfur gases, and many organic and food acids.
Type 405: This type has a lower chromium content combined with added aluminum. This chemical makeup helps prevent hardening when cooled from high temperatures. Typical applications include heat exchangers.
Type 409: One of the least expensive Stainless grades due to its decreased chromium content. This type should only be used for interior or exterior parts in non-critical corrosive environments. Typical applications include muffler stock.
Type 434: This type has an increased Molybdenum content that gives it improved corrosion resistance. Typical applications can include automotive trim and fasteners.
Type 436: This grade has columbium added for corrosion and heat resistance. Most typical applications include deep-drawn parts.
Type 442: Has improved scaling resistance due to the increased Chromium content. Applications can include furnace and heater parts.
Type 446: Even higher chromium content has been added to further improve corrosion and scaling resistance at high temperatures. This grade is very good with oxidation resistance in a sulfuric environment.
Austenitic Stainless Steel
Austenitic Stainless is the most commonly used stainless class. The high Chromium and Nickel content of the grades in this group provide superior corrosion resistance and very good mechanical properties. They cannot be hardened through heat treatment, but can be hardened considerably through cold-working. None of the grades in this class are magnetic.
Standard Grades
The standard grades of austenitic stainless steel contain a maximum of .08% carbon; there is no minimum carbon requirement.
Low Carbon Grades (L Grades)
The “L” grades are used to provide extra corrosion resistance after welding. The letter “L” after a stainless steel grade number indicates low carbon. Carbon levels are kept to .03% or under to avoid carbide precipitation, which can lead to corrosion. Due to the temperatures created during the welding process (which can lead to carbon precipitation) – “L” grades are typically used. Quite commonly, Stainless mills offer these stainless grades as dual certified, such as 304/304L or 316/316L.
High Carbon Grades (H Grades)
Stainless “H” grades have a minimum of .04% carbon and a maximum of .10% carbon. The higher carbon helps retain strength at extreme temperatures. These grades are indicated by the letter “H” after the stainless grade number. The use of this designation would be when the end-use involves an extreme temperature environment.
Type 304: One of the most commonly used (Austenitic) Stainless grades. Its high content of Chromium and Nickel make it a preferred choice when making processing equipment for the chemical (mild chemicals), food/dairy and beverage industries. This grade possesses an excellent combination of strength, corrosion resistance and fabric-ability.
Type 316: This Stainless grade has 18% chromium, 14% Nickel and added Molybdenum; these in combination increase its resistance to corrosion. In particular, it is the molybdenum that is used which helps to control the pit type attack of corrosion. This grade will resist scaling at temperatures up to 1600 F. Type 316 is used in chemical processing, the pulp and paper industry, for food and beverage processing and dispensing and in the more corrosive environments. It is also used in the marine industry due to its resistance to corrosion.
Type 317: Containing a higher percentage of molybdenum than 316, it is used in highly corrosive environments. The Molybdenum content of this grade must be greater than 3%. Commonly used in scrubber systems of air pollution control devices that are used to remove particulates and/or gases from industrial exhaust streams.
Type 321: Contains a Titanium addition of at least five times the carbon content. This addition is made to reduce or eliminate chromium carbide precipitation – resulting from welding or exposure to high temperatures. Used in the Aerospace industry.
Type 347: Has a slightly improved corrosion resistance over type 321 stainless steel in strongly oxidizing environments. Type 347 should be considered for applications requiring intermittent heating between 800ºF (427ºC) and 1650ºF (899ºC), or for welding under conditions which prevent a post-weld anneal.
Duplex (Ferritic-Austenitic) Stainless Steels
Duplex grades are a combination of austenitic and ferritic material. These grades are about twice as strong as the austenitic and ferritic grades. While they do have better toughness and ductility than the ferritic grades, they do not reach the levels of the austenitic grades. Duplex grades have a corrosion resistance very close to the austenitic grades such as 304 and 316. Grade 2205 is the most widely used in the duplex class.
Type 2205: Duplex 2205 is ideally suited for high-pressure and highly corrosive environments. It also has high corrosion and erosion fatigue properties as well as lower thermal expansion and higher thermal conductivity than austenitic. The usage of this grade should be should be limited to temperatures below 315° C, as extended elevated temperature exposure can result in brittle material.
Type 2304: Duplex 2304 is generally used in the same applications in which Alloys 304 and 316L are used. It has corrosion resistance very close or slightly better than austenitic grades 304 and 316, but it has nearly doubled yield strength. It is suited for use in temperatures between -50° and 300° C. This grade has a high mechanical strength and a high resistance to stress corrosion cracking. It has good weldability, machinability, and is easy to fabricate.
Type 2507: Duplex 2507 is a super duplex stainless steel. It is in applications which require exceptional strength and corrosion resistance, such as chemical process, petrochemical, and seawater equipment. This grade has excellent resistance to chloride stress, corrosion cracking, high thermal conductivity, and a low coefficient of thermal expansion. The high chromium, molybdenum, and nitrogen levels provide excellent resistance to pitting, crevice, and general corrosion.
Precipitation-Hardening (PH) Stainless Steels
Precipitation hardening stainless steel can be strengthened and hardened by heat treatment. This offers the designer a unique combination of fabric-ability, strength, ease of heat treatment, and corrosion resistance not found in any other class of material. These grades include 17Cr-4Ni (17-4PH) and 15Cr-5Ni (15-5PH).
Type 17-4: Alloy 17-4 is a chromium-copper precipitation hardening stainless steel that is used for applications requiring high strength and a moderate level of corrosion resistance. It has high strength and good corrosion resistance in all heat treated conditions. This grade can be heat treated in a variety of temperatures; resulting in a wide range of finished properties. This grade should not be used in temperatures above 300° C or very low temperatures.
Type 15-5: This is a variant of the older 17-4 chromium-nickel-copper precipitation hardening martensitic stainless steel. The 15-5 alloy was designed to have greater toughness than 17-4. It is used in applications requiring better corrosion resistance and transverse properties compared to other similar martensitic grades.