The 7 Flow Meters Used in the Oil and Gas Industry
- Share
- Issue Time
- Mar 20,2023
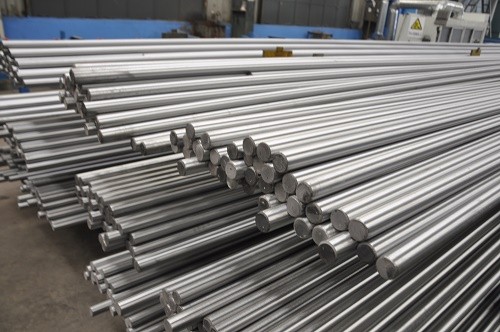
The 7 Flow Meters Used in the Oil and Gas Industry
Over the years, people who are involved in the oil and gas industry have been innovating and creating ways to get accurate measurements. From extracting to delivering these raw materials, everyone in the business has been deeply invested in getting the most accurate measurements possible.
Thus, scientists and engineers have been working long and hard to discover new ways and technologies to make more efficient metering systems. Because of their hard work, the creation of different flow meters materialized, and because of that, the oil and gas industry is still going strong today.
These flow meters are used by industries, particularly gas and oil, to calculate the mass flow rate or volumetric flow rate of fluids. Such an application defines the capacity and type of flow meter. Gases, liquids, and fluids are measured in terms of mass flow rate and volumetric flow rate.
Where and How Do Oil and Natural Gas Form?
Before we tell you the different flow meters that are commonly used in the oil and gas industry, knowing the process of how industries collect raw materials should come first.
Both of these raw materials are present on different geological sources. Mostly, gas and oil fields are present on sedimentary rocks like sandstone and limestone. The main reason is that these materials can easily pass through rocks, making them easier to accumulate. The capacity of the reservoirs found can be determined by its porosity, while the productivity is proportional to their permeability.
To start a flow, they drill inside these rocks, which will make the fluids easier to extract. To either start, increase, or for continual flow, water is pumped inside the rocks, which are commonly located underground. High-pressured water is pumped in these rocks, which will increase the flow rates and increased extraction of fluids. A type of flow meter, called ABB’s electromagnetic flow meter, is used to accurately and precisely measure the water being pumped inside the rocks.
However, there are certain cases where drilling and pumping water is not enough to acquire these substances. Oil or natural gas found on impermeable rocks is mostly unable to form into conventional means. These materials are called ‘unconventional hydrocarbons’, and they include shale oil, coal-bed methane, and shale gas. Because of the rock’s very low permeability, the accumulation should be stimulated to start a flow and enable the extraction process. To do this, a method called ‘hydraulic fracturing’ is necessary.
In hydraulic fracturing, a mixture of sand and water is pumped inside the rocks. Because of the high pressure, small fractures (fissures) are made, which will make the materials free to move inside the foundation. Hydraulic fracturing is done by enabling these fissures to be open for the materials to move, which is what the sand does; opening these fractures, which results in high permeability. To get the precise measurement of the fracturing fluid and the blending of additives in the mix, ABB’s electromagnetic flow meter is used.
Now that we have explained the overview of how the oil and gas industry get these raw substances; the next step is getting to know how they measure it with different types of metering systems.
Coriolis Flow Meters
The technology used in the Coriolis flowmeters is not precisely the newest in terms of measuring the natural substances in the oil and gas industry. The first industrial patent for the Coriolis flowmeter is dated back in the 1950s. However, the start of the application of the said technology in the field is not until 1970. And up until now, nothing has changed although the refinement of the meters for more accurate measurements.
One of the original designs of the flow meter is that it features a single tube with thin walls. It is highly accurate; however, the practicality of the model is the primary concern because of its vibration issues. To address that, the design was changed into a two-tube design instead of one.
Although having gone through different designs, the main principle of the Coriolis flowmeter has never changed. By creating inertia through oscillating tubes as the materials flow through them, the tubes twist. The number of twists is directly proportional to the mass flow rate. This is then measured flow meter transmitters and a sensor to make a linear flow signal.
Using a Coriolis flowmeter has several advantages. One of these is that it is highly accurate. These flow meters are more commonly used to measure a wide range of petroleum products such as crude oil and natural gas. The main gist of the flow meter is that it measures mainly the mass flow rate instead of its volume. It makes it best for measuring petroleum products since the primary concern in measuring these products is the heat rather than the quantity.
Typically, this type of flow meter applies to pipes with a diameter of 1 to 4 inches. But nowadays, larger models have been more available than before. Probably the only downside of Coriolis flowmeters is it is more expensive than other types of metering systems. This can be worth as it is more low maintenance than the other flow meters.
Ultrasonic Flow Meters
Ultrasonic flow meters measure the velocity of the fluid running through a pipe by the use of sound waves. A linear shift in its frequency will be noticeable once the speed of the fluid slowly increases.
Ultrasonic flowmeters can be used for both measuring the velocity of the liquid inside and outside the pipe; inline designs mount the flow meter inside the tube while clamp-on models
measure the speed using transducers. However, clamp-ons are lower in accuracy than inline models. Thus, they are only used to spot checks to get the measurement immediately.
Unlike the Coriolis flow meter, ultrasonic flow meters and other flow meters that are designed specifically for crude oils can be used inline for pipes that have a 20-inch measurement. Also, the clamp-on design is applicable in a lot of different things and is durable. Not to mention, it also has low maintenance requirements.
Thermal Flow Meters
In its primary sense, thermal flow meters measure the speed of the heat that dissipates as it is injected directly into a gas flow stream. Mostly, thermal flow meters are used exclusively for measuring gases.
Heat dissipation varies depending on the composition and the temperature of the gas. Thermal flow meters are the best choice when either of the composition or the temperature is minimized or if that level of accuracy as within acceptable parameters.
Turbine Flow Meters
This type of meter uses a mechanical rotor that is attached to a shaft that is inside the pipe. It is then used to measure the volume of gas, fluid, or vapor that passes through the tube. As the substance passes through the pipe, the rotor spins with its speed depending on how fast the material passes through the pipeline. The rotational speed that results from the spinning of the rotor is determined by the use of sensors or other mechanical methods.
Typically, magnetism is used to let the sensors get reading from the rotor, with the magnet located outside the pipe. With the use of signals, sensors and transmitters determine the volume of the material traveling inside the tube.
Turbine flow meters are cheap in terms of pricing. Also, they give more accurate results when the substance measured is gas or any other material that has no debris at a slow flow rate.
One disadvantage of using a turbine flow meter is that it does not work well with a varying flow as the mechanical parts can wear out significantly and will need immediate replacement. Also, turbine flow meters work best when measuring the mass of a gas with unknown properties.
In addition to its uses, it is also commonly used for billing meters to measure the amount of gas or water in commercial, industrial, and residential buildings. However, in this aspect, it competes with positive displacement flow meters. The latter is more suitable with pipes with a measurement of 1.5 to 10 inches while turbine flow meters are best suited with pipes 10 inches or above in size.
Differential Flow Meters
Like its distant cousin, ultrasonic flow meter, it also measures the volume of the flow that passes through within the pipe. What sets it apart from other flow meters is its use of Bernoulli’s equation. Also, differential flow meters use constriction to slow down the flow and pressure of substance inside the pipe.
As the flow pressure slowly increases, the pressure drop’s size also increases proportionately. The data from this event is transmitted on varying sets of pressure readings. With that information, it calculates the difference in pressure to get the measurement of the volumetric flow.
Differential flow meters are typically low-cost. And different versions for different substances also exist to make accurate measurements of every fluid. Gases are special cases, though, because, to get the precise reading of a particular gas, differential flow meters should be combined with other sensors for different factors like temperature, pressure, the composition of the gas, and the gas’ density.
Although it is an excellent flow meter on its own, industries prefer other types of metering systems. This is mostly due to its inaccuracy when other factors are involved, like temperature, pressure, etc. Also, to get the most accurate measurement of gas, it needs to combine with other sensors or get a different version of a differential flow meter altogether. Because of the mentioned factors, it can be hard to get an accurate reading. It is mainly the reason why the oil and gas industry prefers other types of metering, especially when dealing with gases.
Positive Displacement Flow Meters
There are different types of positive displacement meters: oval gear, piston, rotary, diaphragm, nutating disc, and helical.
Positive displacement meters can be applicable for a wide variety of things that involve commercial, industrial, and residential applications. They are most commonly used to measure gas flow. Turbine flow meters, however, competes with positive displacement flow meters in this aspect. One of its advantages over turbine flow meters is that it is excellent in dealing with a steady flow rate in a pipeline that has a diameter of 10 inches or less.
Both diaphragm and rotary-based positive displacement flow meters are typically used for measuring gas flow. Against competitors like Coriolis flowmeters, the latter is the first choice mainly because positive displacement flow meters do not have the required industry approvals for application in the field.
Vortex Flow Meters
One of the most versatile of flow meters, vortex flow meters, can easily measure gas, liquid, steam flows.
Over the past years, vortex flowmeters lacked the necessary approvals for application in the industry. However, in 2007, the American Petroleum Institute had approved a draft standard for the use of the said flow meter. And since then, several companies in the industry have been actively working with API for further developments regarding this standard and its approval.
The said standard is applied to liquid, steam, and gas flows and was extended in 2010 for further use. Despite having an uncertain future, designs were made explicitly for gas and liquid exists. Vortex flow meters have had a limited impact on the market in recent years, but a steady increase in its preference is present for future companies. However, its effect on the market regarding custody-transfer in natural gas is low because of other competitors like ultrasonic, differential pressure, and turbine flow meters.
Conclusions
There are a lot of technologies readily available for the oil and gas industry to use and adapt. Not to mention that the market has been introducing new types of flow meters waiting for the API’s approval. Due to the different fluids that a lot of industries collect, the need for low cost and maintenance metering systems is on the rise. This had led to creating bigger models of Coriolis flowmeters, making it one of the most used metering systems to date.