440C Stainless Steel Characteristics and Applications
- Share
- Issue Time
- Mar 27,2023
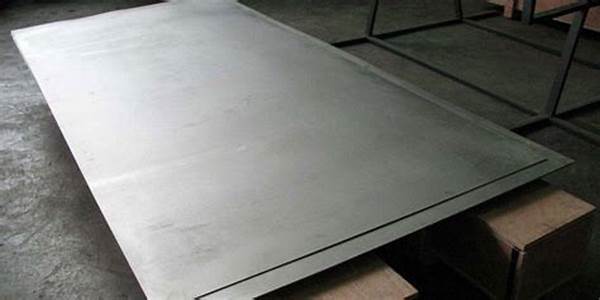
440C Stainless Steel Characteristics and Applications
What is 440C Stainless Steel?
Characteristics of 440C stainless steel
440C has the highest hardness of all stainless and heat resistant steels and is used for nozzles and bearings. 440F is a steel grade that improves the easy cutting properties of 440C steel and is used for automatic lathes. Martensitic stainless steel has the same characteristics of hardening by quenching as alloy steel, so a wide range of different mechanical properties can be obtained by selecting the grade and heat treatment conditions.
440C stainless steel contains C 1.2% carbon, this steel has good rust resistance, is currently imported in mass production of small knives more commonly used, its chromium content of up to 16-18%, is also one of the first stainless steel used for tool making, quite popular. If heat treated as bearing, a deep cooling treatment is generally recommended prior to the tempering operation. Such a deep cooling treatment improves the hardness of the steel and increases wear resistance and dimensional stability. Therefore, deep cooling treatment of 440C is also often used for tool heat treatment.
440C stainless steel chemical composition (%)
C :1.10
Mn :1.00
P :0.03
S :0.010
Cr :17.50
Mo :0.60
Ni :0.60
Cu :0.50
Si :1.00
440C stainless steel applications
It is mainly used for manufacturing bearing parts that work in corrosive environment and strong oxidizing atmosphere without lubrication. 440C has good high temperature dimensional temperature property, so it can also be used as corrosion resistant high temperature bearing steel. In addition, it can also be used to manufacture high quality tools such as medical scalpels, scissors, nozzles, bearings, etc. 440F is a steel grade that improves the easy cutting properties of 440C steel for automatic lathes, and has the same hardening properties as ordinary alloy steel through quenching, so a wide range of different mechanical properties can be obtained by selecting the grade and heat treatment conditions. 440C stainless steel is a modern steel known for its high corrosion resistance, wear resistance, strength and hardness qualities among all stainless steel alloys, up to HRC 60 after heat treatment. 440C has good resistance to corrosion by air, fresh water and weak acids, creating smooth polished surfaces and razor sharp edges in the process of making cutting tools. and razor-sharp edges. This steel is used for cutting tools, rolling bearings, valve seats, high quality sharpening tools, surgical instruments, chisels, ball bearings and production cutting tools including hair clipper blades, surgical blades, daggers and razor blades.
440C Stainless Steel Features
440 steel actually refers to the steel system consisting of 440A, 440B and 440C, but in terms of making cutting tools, 440 steel is generally referred to as 440C. The only difference is that its carbon content is slightly higher (0.65%-0.75% and 0.75%-0.95% for the remaining two steels, respectively). Although the higher carbon content causes the hardness of the cutting tools to be high, the corrosion resistance is slightly reduced. Although these three steels are standard steel grades of the same grade, 440C is in fact more practical than A and B. The other alloy, 440F (UNS S44020), has the same carbon content as 440C. From the current point of view, the use of 440C steel is very common.
Higher hardness and moderate wear resistance, it has the disadvantage of being more sticky and heating up quickly when grinding. It is recommended to use chrome corundum or microcrystalline corundum grinding wheels for grinding. 440C has a very low annealing temperature and the hardness can usually reach HRC45-54 when heat treated as tools and bearings, and HRC56-58 if deep cooling treatment is carried out. corrosion resistance and toughness are very strong, now it is more widely used in hand-made knives and high-quality factory-made tools.