Broad Basics on the World of Metal Finishing
- Share
- Issue Time
- Jun 15,2023
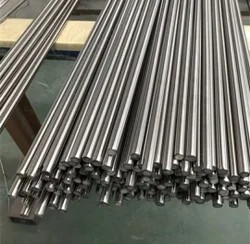
Broad Basics on the World of Metal Finishing
There are a few concepts or processes that are simply vital within the world of metal manufacturing and metalwork, and one of the most notable here is finishing. Finishing is a broad category that speaks to various treatments used to affect a metal’s molecular structure, and offers numerous ways to improve the surface of a metal with specific applications or needs in mind.
Why Metal Finishing is Vital
For those who are just learning about metal finishing, it’s important to understand why the process exists and how it can be beneficial. Finishing is used to improve a metal’s surface qualities, such as resistance to corrosion or oxidation, conductivity, wear and abrasion resistance, reflectivity or other desired attributes.
The aim of any metal finishing process is to create an outer layer that will be better suited for the specific needs of your application. Finishing is also a great way to increase both visual and aesthetic appeal through polishing, coating or other treatments.
For these reasons, finishing is one of the most common treatments done to metal objects, including metal pipes and metal sheets.
Types of Metal Finishing
There are several types of metal finishing out there depending on the application and other factors. These include:
· Grinding: This process uses abrasive materials to smooth the surface of a metal. It can be used for some basic grinding, or in more fine finishing processes such as polishing and honing.
· Plating: Plating involves applying thin layers of metal material on top of a host metal to provide improved characteristics, often related to corrosion resistance or wear resistance.
· Electroplating: One particular type of plating, electroplating involves adding a thin layer of metal material to the surface of another through an electric current.
· Anodizing: Anodizing is another type of metal finishing that uses an electrical current to create a protective layer on the surface of the metal.
· Powder coating: This process involves spraying dry powdered paint onto a metal surface, which will then be heated to form a strong and durable finish.
· Polishing or buffing: This type of metal finishing involves using an abrasive material to create a smooth, shiny surface.
· Painting: While this is not a metal-specific process, painting on metals can offer excellent protection and also create an aesthetically appealing finish.
· Blasting: Sand, glass beads or other materials are used to create a matte finish on certain metals. This allows for a strong, durable finish on the surface of the metal.
· Brushing: Another technique used to give metal objects a glistening finish, this process involves brushing the surface with an abrasive material.
Key Factors To Consider When Selecting A Finish Type
When you’re deciding which type of metal finishing is best for your application, there are several factors that need to be taken into consideration. These include:
· Base metal being used: Different metal finishes are better suited to certain base metals, so be sure to look into which type of finish is best for your particular material. For instance, anodizing is often best for aluminum, while electroplating is usually used on brass or copper.
· Aesthetic needs: What kind of look and feel do you want your metal to have? Keep this in mind when selecting a finish type so that you achieve the desired outcome.
· Protection and durability requirements: Different finishes offer different levels of protection and durability, which is an important factor to consider. For instance, painting can be a great way to protect against corrosion or weathering, while anodizing offers excellent wear and abrasion resistance.
· Cost: Different metal finishes come with different costs associated with them, so it’s important to keep this in mind as well.
By understanding the different types of metal finishing and key factors to consider when selecting a finish type, you can make sure that you choose the right metal solution for your particular application. Not only can this help ensure that you get the desired aesthetic results, but also protect against wear-and-tear or corrosion in the long run.