Wear Resistance of High Carbon and High Chromium Cold Work Die Steel Self-lubricating
- Share
- publisher
- harris
- Issue Time
- Nov 28,2019
Summary
Study on Wear Resistance of High Carbon and High Chromium Series Self-lubricating Cold Work Die Steel
With the rapid development of the mold industry, China has made rapid development in various aspects such as the research and development of cold work mold steel materials, although the new Cr8 series cold work mold steel has both high toughness and high alloy cold work alloy steel. The advantages of high strength and good wear resistance of the die steel basically solve the problems of early brittle fracture, insufficient toughness, or deformation failure of commonly used cold work die steels on the market, but the problem of wear or bite failure of cold work die materials is still difficult to solve. . In order to extend the life of the mold and solve the wear problem under the premise of ensuring strong and toughness, this article is based on high-carbon high-chrome self-lubricating cold-working die steel as the research material, combining the anti-wear performance under various friction and wear test methods and its resistance to Comparative analysis of wear mechanism. The results show that the friction coefficient of high-carbon and high-chrome self-lubricating cold-working die steel is much lower than that of other traditional steels, showing excellent anti-wear properties, and great engineering application value, but its anti-friction and self-lubricating The mechanism and control technology of self-lubricating phase have not been systematically studied.
At present, this kind of self-lubricating cold-working die steel is a new concept. Its research and production are still in the undisclosed stage. The research on its self-lubricating mechanism and control is not clear. The literature of similar alloy system steels aims to review the role played by S, Cu, Al and other alloying elements in new cold-working die steels, and to reveal the inherent relationship between different forms of friction and wear properties and microstructures to reveal self-lubrication The mechanism of wear reduction of steel phases in steel, and briefly describes the method of self-lubricating phase control in self-lubricating steel, and discusses the influence rules and mechanisms of heat treatment process on the type, shape, size and distribution behavior of self-lubricating phases.
The role of main alloying elements in self-lubricating steel
This article uses a high-carbon high-chromium series self-lubricating cold-working die steel. In order to ensure sufficient hardenability and reduce primary carbide segregation, the minimum Cr is controlled at about 8%; by adding a certain amount of W and Mo to achieve two Secondary hardening, addition of Ni and Al to form Al3Ni intermetallic compounds, and the secondary hardening is compensated by its precipitation; the added Cu can be used as a nucleation core to reduce the precipitation temperature of Al3Ni to near the secondary hardening temperature, and the most important is to add S The sulfide formed acts as a self-lubricating phase, improving processability and improving wear resistance. In view of this, the materials reviewed in this article are mainly Fe-1.0% C-8.3% Cr-Ni-Mo-W-Al-Cu-S high-carbon and high-chromium self-lubricating cold-working die steel with alloying elements such as S and Cu .
Analysis of anti-wear mechanism of self-lubricating steel
In this paper, three different test methods are selected. The first method is to use the test method, that is, to directly evaluate the anti-wear performance of self-lubricating cold-working die steel directly under actual working conditions. In the second and third tests, The method of sample test is used to study and analyze the anti-wear mechanism.
The first test uses an 80-ton crank press to perform a hat-shaped bending test as shown in the figure below. The mold is an S-MAGIC self-lubricating cold-work mold steel developed by a foreign factory. The test results of the test showed that no scratches occurred in the S-MAGIC steel after 3 strokes, while other mold materials had more obvious scratches. The surface roughness of S-MAGIC steel stampings is small, and its friction is also small, which avoids the cold welding of worn particles on the workpiece surface to form a new metal surface layer, which shows that the steel has a good anti-wear effect.
The second test uses the ball-and-disk abrasion method. As shown in the figure below, the disk sample is made of the mold used in the above-mentioned hat-bending test. The results show that the friction coefficient of S-MAGIC steel is significantly lower than that of other traditional steels. It can be clearly seen from the above two types of friction and abrasion tests that the surface abrasion condition and friction coefficient of S-MAGIC steel are much smaller than those of other traditional steel types. It is concluded that the addition of alloy elements such as S and Cu can be generated in situ in the steel Self-lubricating phase, which greatly improves the wear resistance of steel.
As can be seen from the figure below, for the initial friction coefficient, S-MAGIC steel and -Al steel (Al removal steel) have the lowest, -WMo steel and -Cu steel have the highest, and the higher value of -WMo steel is mainly due to the absence of W and Mo. Elementary formation of secondary hardening results in lower hardness. The high friction coefficient of -Cu steel is mainly caused by the corrosion and wear caused by the addition of S. In comparison, the addition of S and Cu significantly reduces the friction coefficient of steel.
Therefore, based on the above experimental results, it can be known that S can obtain excellent workability of steel. The mechanism is mainly that S combines with W and Mo in steel to form a finely dispersed MxSy metal sulfide self-lubricating phase in situ, and its crystals The structure is a hexagonal crystal structure, which is easy to slide along the densely packed surface for plastic deformation, so it has good lubricity, so it significantly reduces the friction factor between the friction pairs and improves the anti-wear performance. In addition, during metal cutting or a certain load contact process, a FeS lubricating mold layer is formed in the contact area S and Fe where friction generates a high temperature, which reduces the material adhesion between the friction pairs and further reduces adhesive wear.
The third test adopts the pin-disk wear method. The pin uses three test materials, one is standard D2 steel, and the other two are + Cu 8% Cr steel and + CuAl 8% Cr steel. It can be seen from the results that the initial friction coefficients of + Cu steel and + CuAl steel are slightly lower than those of standard D2 steel. And for critical wear critical slip distance, CuAl steel is the smallest, followed by + Cu steel, D2 steel is the largest, and + CuAl steel with the highest hardness has the longest critical slip distance, so + CuAl steel has the best wear resistance.
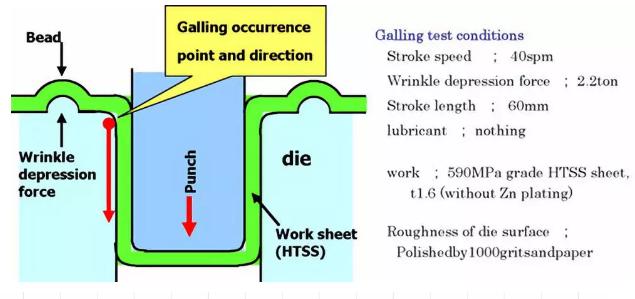
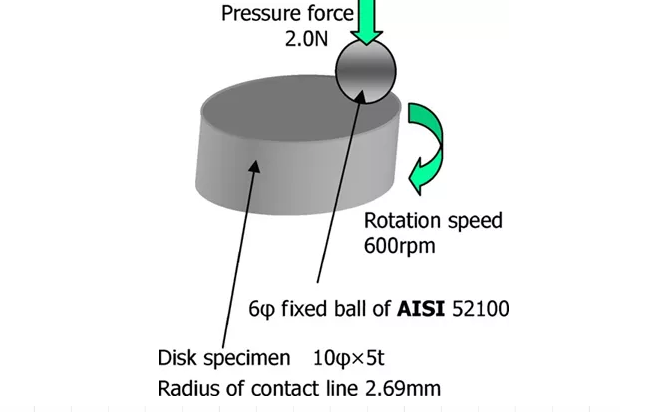
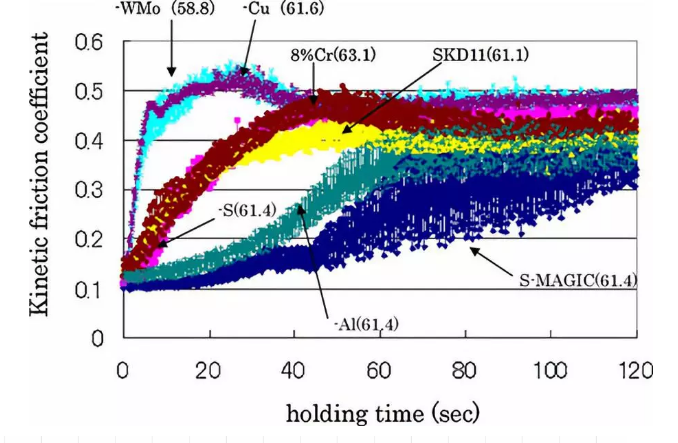
After comprehensive analysis of the above tests, the results obtained are almost the same. The addition of alloying elements such as S and Cu in the steel can significantly reduce the friction coefficient of the steel, and greatly improve the wear resistance of the steel through its self-lubricating effect, thereby improving the service of the mold. life.
Self-lubricating cold-working die steel, as a new type of high-end cold-working die steel, has a good ratio of strength and toughness on the surface and excellent wear resistance. It is expected to solve the problem of wear failure of traditional cold-working molds and minimize heat treatment deformation. After the heat treatment of the mold, the dimensional accuracy is high, which is extremely useful for manufacturing sophisticated and sophisticated high-end cold stamping molds. This steel plays a vital role in the final domestic production of high-end molds for automotive parts.
(1) High-carbon high-chrome self-lubricating cold-working die steel has lower friction coefficient and higher wear resistance than traditional cold-working die steel.
(2) It can be known from the experiment of controlling the chemical composition variables that the excellent wear resistance of the steel is mainly attributed to the addition of S and Cu, forming a sulfide self-lubricating phase.
(3) The wear resistance of this steel can be improved by secondary hardening to precipitate a large number of secondary carbides, smaller carbide size and larger degree of dispersion distribution.
However, the research on the lubrication mechanism of self-lubricating cold-working die steel is still blank, especially the quantitative relationship between the phase types and contents of S, Cu, Ni, Al and other elements in steel and the microstructure and properties is a future study.