Two corrosion classifications for metallic materials
- Share
- publisher
- harris
- Issue Time
- Apr 30,2020
Summary
Two corrosion classifications for metallic materials
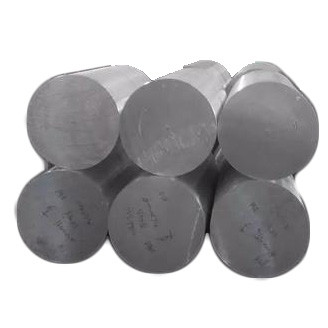
According to the mechanism by which corrosion occurs, it can be divided into three main categories: chemical corrosion, electrochemical corrosion and physical corrosion.
1. Chemical Corrosion
Chemical corrosion is the damage caused by a purely chemical interaction between a metal surface and a non-electrolyte directly. Sulfur corrosion of metals in high temperature gases, high temperature oxidation of metals are chemical corrosion.
2. Electrochemical Corrosion
Electrochemical corrosion refers to the damage caused by the electrochemical reaction of a metal surface with an ion-conducting medium. Electrochemical corrosion is the most common and common type of corrosion, such as corrosion of metals in the atmosphere, seawater, soil and various electrolyte solutions.
3. Physical Corrosion
Physical corrosion refers to the destruction of a metal due to pure physical dissolution. It is characterized by a "cutting" effect on the metal material when the metal with a low melting point dissolves into the metal material. Since metal with a low melting point is generally of low strength, it will preferentially fracture under stress, thus becoming a source of cracking in metal materials. It should be said that such corrosion is not uncommon in engineering.
By corrosion pattern, it can be divided into three main categories: comprehensive corrosion, local corrosion and stress corrosion.
1. General Corrosion
Total corrosion, also known as uniform corrosion, is corrosion that occurs to essentially the same extent over a larger area of pipe. Uniform corrosion is the least dangerous type of corrosion.
(1) The mechanical strength and service life of the material are often ensured by giving a sufficient amount of corrosion margin during construction.
(2) uniform corrosion common unit time corrosion media on the depth of corrosion of metal materials or metal components of the wall thickness reduction (called corrosion rate) to assess.SH3059 standard provides that: corrosion rate does not exceed 0.05mm / a material is fully corrosion-resistant materials; corrosion rate of 0.05 ~ 0.1mm / a material is corrosion-resistant materials; corrosion rate of 0.1 ~ 0.5mm / a material is still corrosion-resistant materials; corrosion rate of more than 0.5mm / a material is not corrosion-resistant materials.
2. Local Corrosion
Local corrosion, also known as non-uniform corrosion, its hazard is far greater than uniform corrosion, because uniform corrosion is easy to be detected, easy to guard against, while local corrosion is difficult to predict and prevent, often in the absence of precursors, so that metal components suddenly damaged, resulting in major fire or personal injury accidents. Localized corrosion is widespread, with uniform corrosion accounting for 17.8% of the overall corrosion and localized corrosion for about 80%.
3. Stress Corrosion
Fracture breakage of metallic materials under the combined action of tensile stress and a specific corrosion medium is called stress corrosion breakage. Stress corrosion ruptures occur over a long or short period of time, ranging from a few days to several years, indicating that stress corrosion ruptures usually have a long or short gestation period.
Stress corrosion cracks are dendritic and develop roughly in the direction perpendicular to the tensile stress. The microscopic morphology of the crack is trans-crystalline, inter-crystalline (along the grain), and a mixture of both.Sources of stress, for pipes, welding, cold working and residual stresses during installation are the main ones.
Not any combination of metal and medium causes stress corrosion rupture. Among these metals, stress corrosion rupture occurs only in certain specific corrosion environments. Table 1 lists the combinations of pipe metal materials and corrosion environments that are susceptible to stress corrosion cracking.